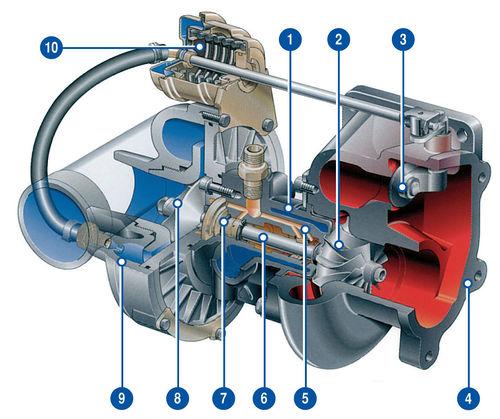
Funcionamiento de los turbocompresores
Los turbocompresores se utilizan comúnmente para mejorar el rendimiento de los motores de gasolina y diésel. Su durabilidad depende del uso adecuado.
Los turbocompresores se utilizan comúnmente para aumentar el rendimiento de los motores de gasolina y diésel. El principio de su funcionamiento es conectar la turbina de gases de escape con un rotor que comprime el aire inyectado en los cilindros.
El turbocompresor tiene una serie de ventajas, entre ellas: un diseño simple, la ausencia de un accionamiento adicional y un costo de fabricación relativamente bajo. El dispositivo también tiene inconvenientes, como un retraso entre el momento en que el conductor presiona el acelerador y la respuesta de la turbina, comúnmente denominado "retraso del turbo", y es susceptible a un mal funcionamiento. Agujero turbo causado la incapacidad del compresor para adaptarse de forma independiente a los cambios en la velocidad y la carga del motor. Ya existen soluciones para mejorar la adaptabilidad de los turbocompresores. Se trata de válvulas de derivación que dirigen el exceso de gases de escape hacia el lado del escape y turbocompresores técnicamente más avanzados con geometría de turbina variable.
En la práctica operativa, lo más importante para el usuario de un automóvil es el conocimiento de las condiciones que tienen un impacto significativo en la duración del funcionamiento sin problemas de un turbocompresor. Primero, el rotor del turbocargador tiene una cierta masa y dimensiones, así como un momento de inercia de masa asociado. Durante la operación, el rotor acelera a una velocidad de 100 - 120 mil rpm. Esto es 10 veces más rápido que el motor de un automóvil de Fórmula 1. Por lo tanto, el rotor de la turbina se equilibra con precisión y su cojinete lubrica el aceite suministrado por la bomba de alimentación del motor. Cuando se opera un turbocompresor, además del mantenimiento, la técnica de conducción es de gran importancia.
Para evitar la entrada de suciedad, el aire de admisión debe mantenerse limpio cambiando el filtro periódicamente. Cualquier cambio en el equilibrio, como depósitos de suciedad, a estas altas velocidades contribuye al desgaste prematuro de los rodamientos. Se debe prestar especial atención al medio refrigerante y lubricante, observando los intervalos de cambio de aceite del motor. Además, no utilice un aceite de una clase de calidad inferior a la recomendada por el fabricante del automóvil. Los experimentos con el cambio del tipo de aceite, la clase de viscosidad y la calidad afectan negativamente al motor y sus unidades. Un aumento en el grado de contaminación del aceite, la pérdida de sus propiedades lubricantes y protectoras afecta negativamente la durabilidad de los cojinetes y el estado de todo el motor. En unidades con alto kilometraje, “tomando” aceite, su nivel debe ser revisado regularmente y reabastecido.
Después de arrancar el motor de combustión interna durante algún tiempo (más corto en verano, más largo en invierno), el aceite no fluye hacia varios mecanismos, incluidos los cojinetes del compresor. Durante este período, se lubrican con una fina capa pegajosa, debido a la viscosidad del lubricante. Por lo tanto, después de arrancar un motor frío, se deben evitar aceleraciones bruscas del gas y arranques bruscos. Esta forma de conducción hace que los rodamientos estén insuficientemente lubricados durante algún tiempo, lo que reduce su vida útil. Por otro lado, durante la conducción después de calentar la unidad de potencia, es recomendable mantener el motor funcionando en el rango de velocidades medias y altas. El apagado adecuado del motor es muy importante para la longevidad del compresor. Después del final del viaje, la bomba de aceite deja de funcionar. No suministra una porción de aceite nuevo a los cojinetes de la turbina, cuyo rotor acelerado continúa girando a una velocidad tremenda durante varios segundos. Durante este tiempo, el aceite que lubrica los cojinetes se calienta mucho, se carboniza, se forman partículas que rayan las pistas de rodamiento hechas con precisión, lo que conduce a su destrucción. Cuando haga funcionar un motor turboalimentado, espere unos segundos antes de apagarlo. En este momento, la velocidad de la turbina disminuye y se reduce la posibilidad de dañar los cojinetes.
El período de funcionamiento sin problemas de un turbocompresor depende en gran medida del modo de funcionamiento. Sin embargo, debe enfatizarse que hubo una serie de dispositivos que fueron mal desarrollados por los fabricantes y fallaron después de un período relativamente corto. Un signo típico de daño del turbocompresor son las vibraciones que se sienten claramente en el lugar de su instalación. En caso de daño severo, se escucha una fricción de metal contra metal, sale una gran cantidad de humo blanco por el tubo de escape, el automóvil aún no acelera.
Los turbocompresores dañados se pueden regenerar. Los talleres especializados cuentan con los conocimientos, la experiencia y los kits de reparación adecuados. El costo de una regeneración típica es, dependiendo del tamaño de la turbina, de 800 a 2000 PLN y varias veces más bajo que el precio de un nuevo dispositivo.
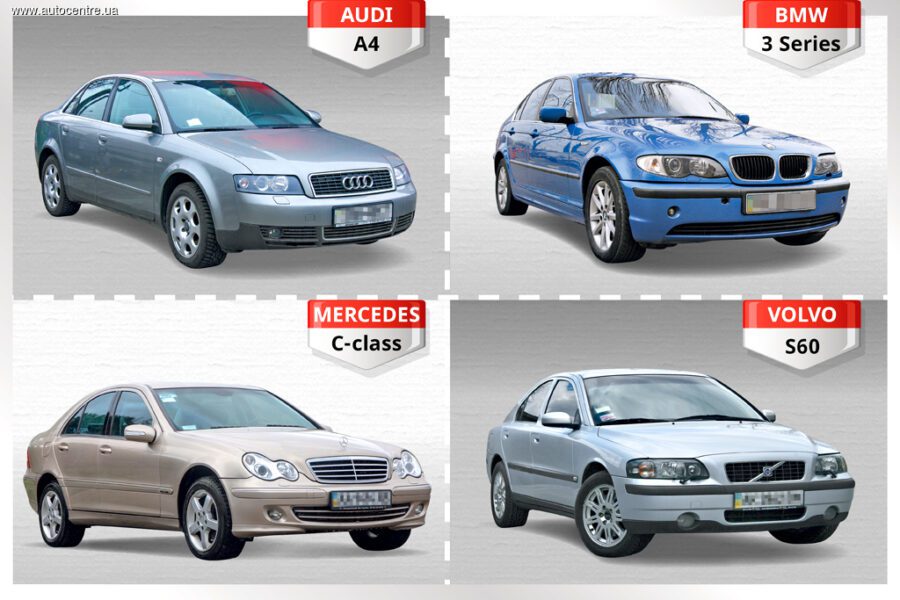
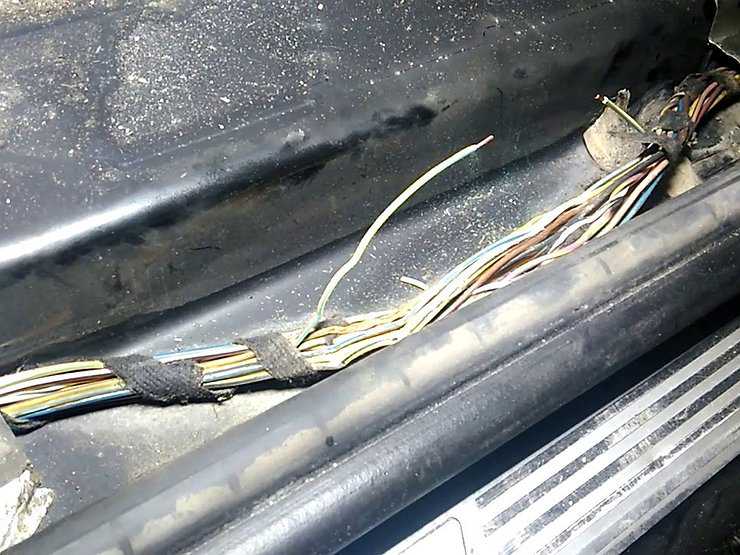