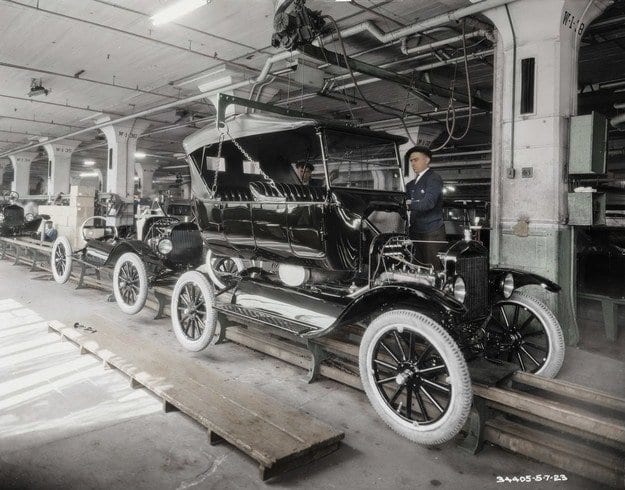
Quién movió el transportador
Las líneas de producción están funcionando nuevamente, y esta es una razón para recordar a su creador.
7 de octubre de 1913 en uno de los pasillos de la planta automotriz de Highland Park. Ford lanza la primera línea de producción de automóviles del mundo. Este material es una expresión de respeto por los procesos de fabricación innovadores creados por Henry Ford, quien revolucionó la industria automotriz.
La organización de la producción de automóviles hoy en día es un proceso muy complejo. El ensamblaje de un automóvil en la fábrica es el 15% del proceso total de producción. El 85 por ciento restante involucra la producción de cada una de las más de diez mil piezas y su premontaje en unas 100 de las unidades productivas más importantes, que luego son enviadas a la línea de producción. Este último lo lleva a cabo una gran cantidad de proveedores (por ejemplo, 40 en VW) que llevan a cabo una cadena coordinada muy compleja y muy eficiente de procesos de producción, incluidas entregas precisas y oportunas (el llamado proceso justo a tiempo). ) de componentes y proveedores. primer y segundo nivel. El desarrollo de cada modelo es solo una parte de cómo llega a los consumidores. Un gran número de ingenieros están involucrados en la organización del proceso de producción que tiene lugar en un universo paralelo, incluyendo acciones desde coordinar el suministro de componentes hasta su montaje físico en una fábrica con la ayuda de personas y robots.
El desarrollo del proceso de fabricación se debe a casi 110 años de evolución, pero Henry Ford hizo la mayor contribución a su creación. Es cierto que cuando creó la organización actual, el Ford Modelo T que comenzó a instalarse era extremadamente simple, y sus componentes eran producidos casi en su totalidad por la propia empresa, pero cada campo de la ciencia tiene sus pioneros que sentaron las bases casi a ciegas. . Henry Ford quedará para siempre en la historia como el hombre que motorizó Estados Unidos, mucho antes de que sucediera en Europa, al combinar un automóvil simple y confiable con una producción eficiente que redujo los costos.
Пионер
Henry Ford siempre creyó que el progreso humano estaría impulsado por el desarrollo económico natural basado en la producción, y odiaba todas las formas especulativas de ganancia. Como era de esperar, el oponente de tal comportamiento económico será un maximalista, y la búsqueda de la eficiencia y la creación de una línea de producción es parte de su historia de éxito.
En los primeros años de la industria automotriz, ingenieros calificados y usualmente talentosos ensamblaban cuidadosamente los automóviles en humildes talleres artesanales. Para ello, utilizan máquinas conocidas hasta ahora para el montaje de coches y bicicletas. En general, la máquina está en una posición estática y los trabajadores y las partes se mueven a lo largo de ella. Las prensas, taladros, máquinas de soldar se agrupan en diferentes lugares, y los productos y componentes terminados individuales se ensamblan en bancos de trabajo, y luego deben “viajar” de un lugar a otro y al propio automóvil.
El nombre de Henry Ford no se encuentra entre los pioneros de la industria automotriz. Pero fue a través de la combinación creativa de las habilidades únicas de administración, organización y diseño de Henry Ford que el automóvil se convirtió en un fenómeno de masas y motorizó la nación estadounidense. Debe su estatus privilegiado a él y a docenas de otros estadounidenses de mentalidad progresista, y el Modelo T de principios del siglo XX le dio un carácter tangible al cliché actual de que un automóvil puede ser una necesidad, no necesariamente un lujo. El automóvil que juega el papel principal en esto, el Modelo T, no brilla con nada especial, excepto por una increíble ligereza y resistencia. Sin embargo, los métodos de Henry Ford para producir este automóvil de manera tan eficiente se convirtieron en la base de una nueva ideología técnica revolucionaria.
Para 1900, había más de 300 empresas fabricando vehículos con motores de combustión interna en el mundo, y los países líderes en este negocio eran Estados Unidos, Francia, Alemania, Inglaterra, Italia, Bélgica, Austria y Suiza. En ese momento, la industria petrolera se estaba desarrollando a un ritmo muy rápido, y ahora Estados Unidos no solo era un importante productor de oro negro, sino también un líder tecnológico en esta área. Esto crea una aleación suficientemente estable como para descartar el desarrollo de la industria estadounidense.
Coche del pueblo americano
En algún lugar de esta confusión, aparece el nombre de Henry Ford. Frente a la oposición de los socios de su primera empresa por su deseo de producir un automóvil práctico, confiable, barato y de producción, en 1903 fundó su propia empresa, a la que llamó Ford Motor Company. Ford construyó un automóvil para ganar la carrera, puso a un ciclista de ocho días al volante y recaudó fácilmente $ 100 de inversionistas benevolentes para su puesta en marcha; los hermanos Dodge acuerdan suministrarle motores. En 000, estaba listo con su primer automóvil de producción, al que llamó Ford Modelo A. Después de lanzar varios modelos caros, decidió volver a su idea original de crear un automóvil popular. Al comprar parte de las acciones de sus accionistas, adquiere suficientes capacidades financieras y posiciones en la empresa para iniciar su propia producción.
Ford es un pájaro raro incluso para la comprensión liberal de los estadounidenses. Cosquilloso, ambicioso, tenía sus propias ideas sobre el negocio del automóvil, que en ese momento diferían significativamente de las opiniones de sus competidores. En el invierno de 1906, alquiló una habitación en su planta de Detroit y pasó dos años con sus colegas diseñando y planificando la producción del Modelo T. El automóvil que finalmente llegó a existir como resultado del trabajo secreto del equipo Ford cambió . imagen de América para siempre. Por $ 825, un comprador del Modelo T puede obtener un automóvil que pesa solo 550 kg con un motor de cuatro cilindros de 20 hp relativamente potente que es fácil de conducir gracias a una transmisión planetaria de dos velocidades operada por pedal. Sencillo, fiable y cómodo, un coche pequeño hace las delicias de la gente. El Modelo T también fue el primer automóvil estadounidense fabricado con acero de vanadio más liviano, que era desconocido para otros fabricantes extranjeros en ese momento. Ford trajo este método de Europa, donde se utilizó para fabricar limusinas de lujo.
En los primeros años, el Modelo T se producía como todos los demás automóviles. Sin embargo, el creciente interés en él y la creciente demanda impulsaron a Ford a comenzar a construir una nueva planta, así como a organizar un sistema de producción más eficiente. En principio, no busca buscar un préstamo, sino financiar sus empresas con sus propias reservas. El éxito del automóvil le permitió invertir en la creación de una planta única en Highland Park, bautizada por el propio Rockefeller, cuyas refinerías son el criterio para la producción más moderna "el milagro industrial de su tiempo". El objetivo de Ford es hacer que el automóvil sea lo más liviano y simple posible, y comprar piezas nuevas es más rentable que repararlas. Un modelo T simple consta de un motor con una caja de cambios, un marco y un cuerpo simples, y dos ejes elementales.
7 octubre 1913 ciudad
En los primeros años, la producción en esta planta de cuatro pisos se organizaba de arriba hacia abajo. "Desciende" del cuarto piso (donde se ensambla el marco) al tercer piso, donde los trabajadores colocan motores y puentes. Después de que el ciclo termina en el segundo piso, los autos nuevos suben por la rampa final más allá de las oficinas en el primer piso. La producción aumentó bruscamente en cada uno de los tres años, de 19 en 000 a 1910 en 34, alcanzando la impresionante cifra de 000 unidades en 1911. Y esto es solo el comienzo, porque Ford ya amenaza con "democratizar el automóvil".
Pensando en cómo crear una producción más eficiente, accidentalmente termina en un matadero, donde observa una línea móvil para cortar carne. La carne de la canal se cuelga de ganchos que se mueven a lo largo de los rieles, y en diferentes lugares del matadero, los carniceros la separan hasta que no queda nada.
Entonces se le ocurrió una idea y Ford decidió invertir el proceso. En otras palabras, esto significa crear una línea de producción principal en movimiento, que es alimentada por líneas adicionales conectadas a ella por acuerdo. El tiempo importa, cualquier retraso en cualquiera de los elementos periféricos ralentizará al principal.
El 7 de octubre de 1913, el equipo de Ford creó una línea de ensamblaje simple para el ensamblaje final en una gran sala de producción, que incluía un cabrestante y un cable. Ese día, 140 trabajadores se alinearon a unos 50 metros de la línea de producción y la máquina fue arrastrada por el piso con un cabrestante. En cada estación de trabajo, se le agrega una parte de la estructura en un orden estrictamente definido. Incluso con esta innovación, el proceso de montaje final se reduce de más de 12 horas a menos de tres. Los ingenieros asumen la tarea de perfeccionar el principio del transportador. Experimentan con todo tipo de opciones: con trineos, pistas de tambores, cintas transportadoras, chasis de remolque en un cable e implementan cientos de otras ideas. Al final, a principios de enero de 1914, Ford construyó el llamado transportador de cadena sin fin, a lo largo del cual se trasladó el chasis a los trabajadores. Tres meses después, se creó el sistema man high, en el que todas las piezas y la cinta transportadora están ubicadas a la altura de la cintura y organizadas para que los trabajadores puedan realizar su trabajo sin mover las piernas.
El resultado de una brillante idea
Como resultado, ya en 1914, 13 trabajadores de la Ford Motor Company ensamblaron 260 automóviles en números y palabras. A modo de comparación, en el resto de la industria automotriz, 720 trabajadores producen 66 automóviles. En 350, Ford Motor Company produjo 286 Model T, 770 cada uno. En 1912, la producción del Modelo T aumentó a 82 y el precio cayó a $388.
Muchos acusan a Ford de convertir a las personas en máquinas, pero para los industriales el panorama es completamente diferente. La gestión y el desarrollo extremadamente efectivos permiten que aquellos que pueden participar en la organización del proceso, y los trabajadores menos educados y poco capacitados, participen en el proceso en sí. Para reducir la rotación, Ford tomó una decisión audaz y en 1914 aumentó su salario de $2,38 al día a $1914. Entre 1916 y 30, en el apogeo de la Primera Guerra Mundial, las ganancias de la compañía se duplicaron de $60 millones a $XNUMX millones, los sindicatos buscaron interferir en los asuntos de Ford y sus trabajadores se convirtieron en compradores de sus productos. Sus compras devuelven efectivamente una parte de los salarios del fondo, y el aumento de la producción mantiene bajo el valor del fondo.
Incluso en 1921, el Modelo T poseía el 60% del mercado de automóviles nuevos. En ese momento, el único problema de Ford era cómo producir más de estos autos. Comienza la construcción de una enorme planta de alta tecnología, que introducirá un método de producción aún más eficiente: el proceso justo a tiempo. Pero esa es otra historia.
Texto: Georgy Kolev
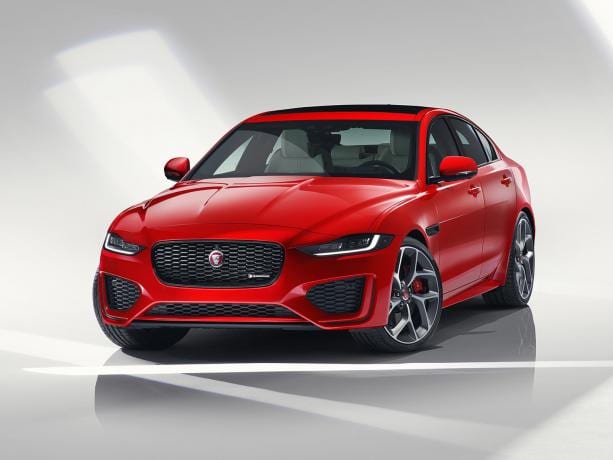
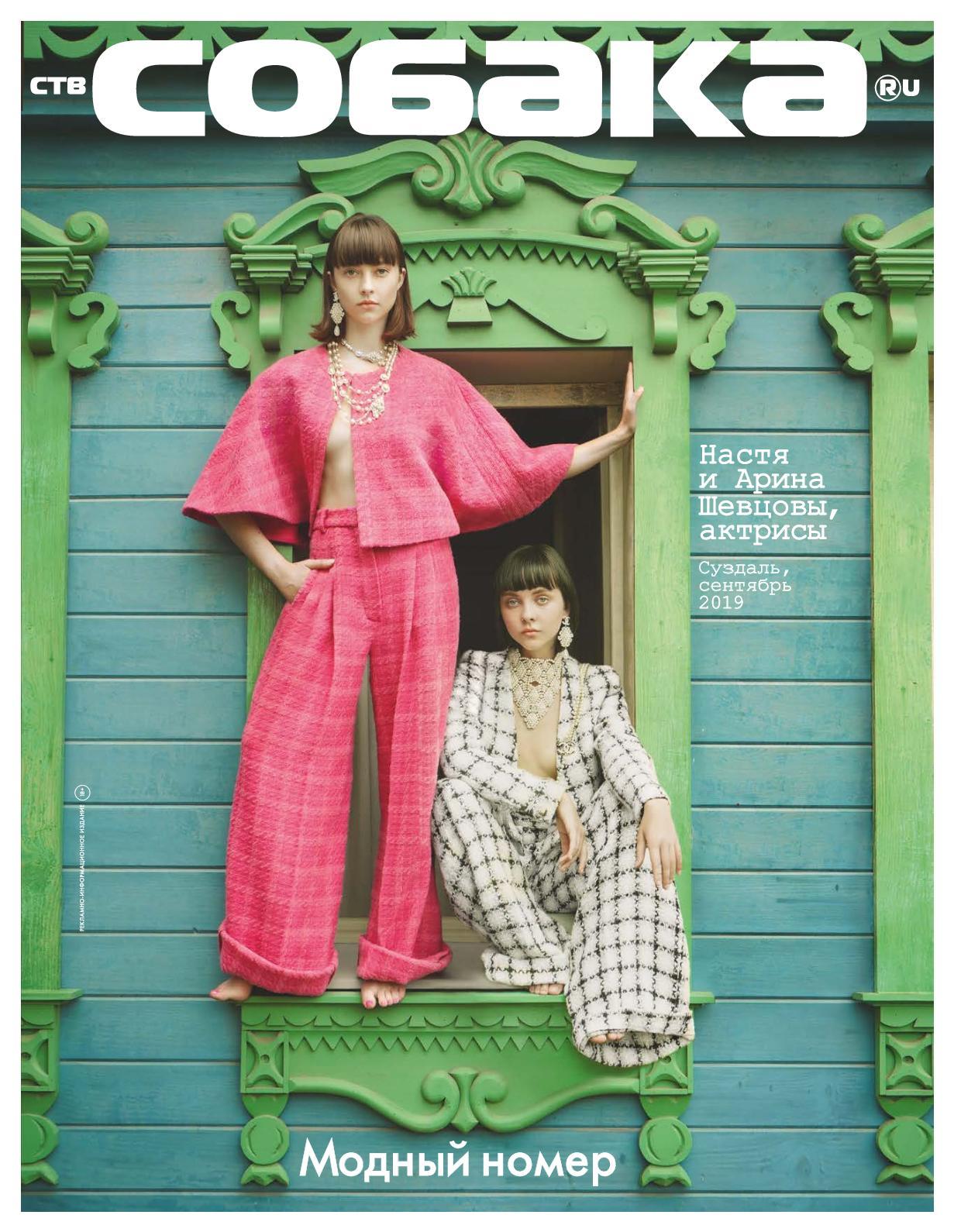