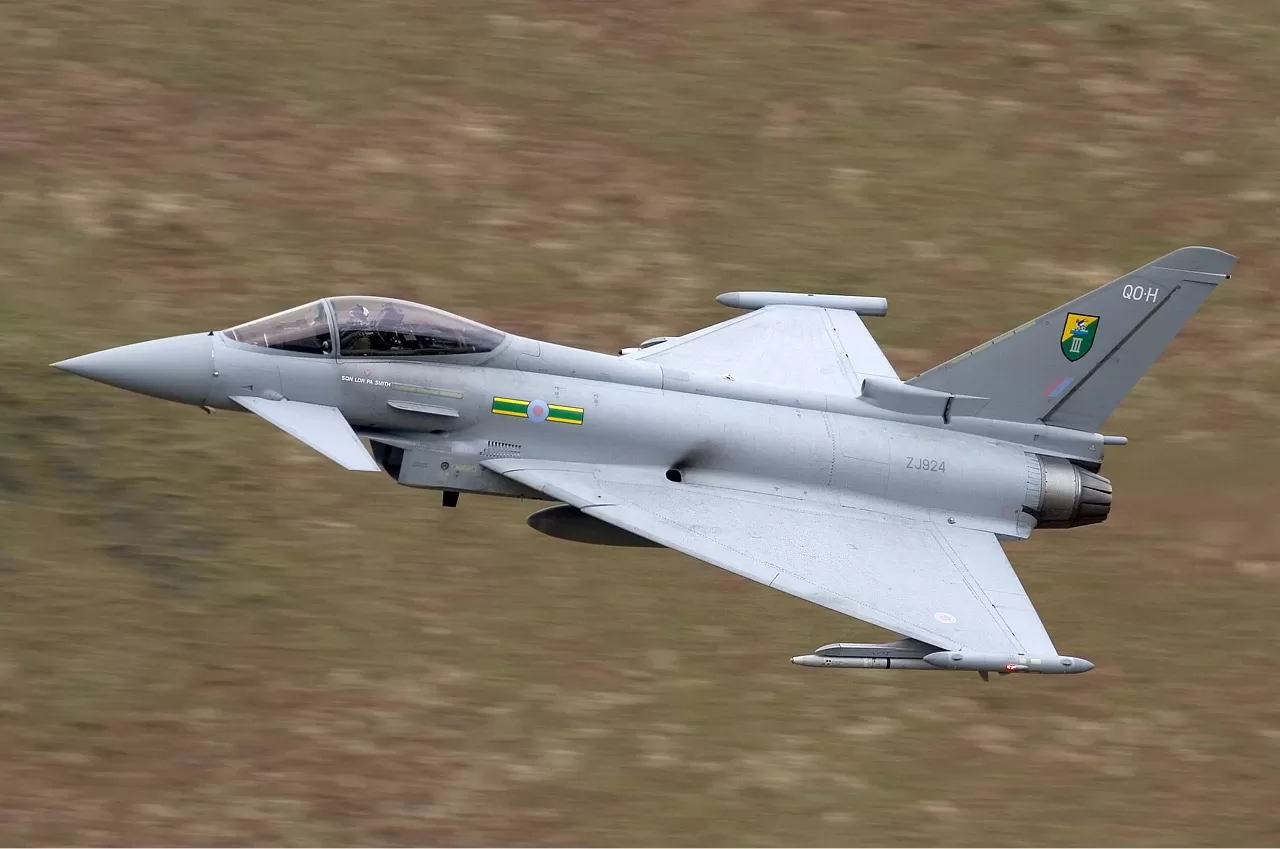
Eurofighter tifón
El Eurofighter combina una maniobrabilidad muy alta con aviónica avanzada, lo que lo convierte en uno de los cazas más modernos y eficientes del mundo.
El consorcio europeo Eurofighter quiere participar en la licitación para el suministro de un caza polivalente (el programa “Harpia”) para Polonia, ofreciendo su caza Eurofighter Typhoon. La ventaja competitiva debe garantizarse mediante consorcios, transferencia de tecnología y creación de empleo en Polonia.
El programa Eurofighter es el programa de defensa europeo más grande de la historia. Hasta ahora, nueve usuarios han pedido 623 cazas de este tipo, incluidos: Arabia Saudita - 72, Austria - 15, España - 73, Qatar - 24, Kuwait - 28, Alemania - 143, Omán - 12, Italia - 96 y Estados Unidos. estados Unido - 160. Además, el 9 de marzo de este año, Arabia Saudita anunció su intención de comprar 48 Eurofighters adicionales, y se están negociando más contratos.
Los países incluidos en el consorcio Eurofighter GmbH dividieron su participación en el mismo de la siguiente manera: Alemania y Reino Unido un 33 % cada uno, Italia un 21 % y España un 13 %. Las siguientes empresas participaron en el trabajo directo: Alemania - DASA, luego EADS; Gran Bretaña - British Aerospace, luego BAE Systems, Italia - Alenia Aeronautica y España - CASA SA. Tras una mayor transformación industrial, Airbus Defence and Space (ADS) adquirió más del 46 % de las acciones en Alemania y España (con las divisiones nacionales de Airbus en Alemania en un 33 % y Airbus en España en un 13 %), BAE Systems permaneció como contratista en el Reino Unido y BAE Systems en Italia, hoy es Leonardo SpA
Los componentes principales del fuselaje se fabrican en siete fábricas diferentes. En el Reino Unido, la antigua planta de English Electric en Samlesbury, más tarde propiedad de BAe y BAE Systems, se vendió en 2006 al fabricante estadounidense de estructuras aeronáuticas Spirit AeroSystems, Inc. de Wichitia. La sección de cola del fuselaje todavía se fabrica aquí para la mitad de los Eurofighter. La planta principal de Wharton, donde se lleva a cabo el ensamblaje final de los Eurofighter para el Reino Unido y Arabia Saudita, también fue propiedad de English Electric y, desde 1960, de British Aircraft Corporation, que se fusionó con Hawker Siddeley en 1977 para formar British Aerospace, hoy Sistemas BAE. Warton también fabrica fuselajes delanteros, cubiertas de cabina, empenaje, joroba trasera y estabilizador vertical, y flaps internos. También había tres fábricas en Alemania. Algunos componentes se fabricaron en Aircraft Services Lemwerder (ASL) ubicado en Lemwerder cerca de Bremen, cuyas fábricas antes eran propiedad de Vereinigte Flugtechnische Werke (VFW) de Bremen, una empresa formada a partir de la fusión de Focke-Wulfa con Weserflug de Lemwerder. pero en 2010 se cerró esta empresa y se transfirió la producción a otras dos plantas. La otra es la planta de Augsburg, anteriormente propiedad de Messerschmitt AG, y desde 1969 de Messerschmitt-Bölkow-Blohm. Como resultado de fusiones posteriores, esta planta pasó a ser propiedad de DASA, posteriormente de EADS, y ahora forma parte de Airbus Defence and Space como filial de Premium AEROTEC. La planta principal para la producción de ADS está ubicada en Manching entre Munich y Nuremberg, donde se lleva a cabo el ensamblaje final de los cazas Eurofighter alemanes, también se construyeron cazas para Austria. Ambas plantas alemanas fabrican la parte central del fuselaje, completan las instalaciones hidráulicas y eléctricas, así como el sistema de control.
En Italia, los elementos estructurales del fuselaje se fabrican en dos fábricas. La planta de Foggia pertenece a la división de estructuras de aviación - Divisione Aerostrutture. Por otro lado, la planta de Turín, donde se realiza el montaje final de los Eurofighter para Italia y los cazas para Kuwait, pertenece a la división de aviación - Divisione Velivoli. Estas fábricas producen el resto del fuselaje trasero, y para todas las máquinas: el ala izquierda y los flaps. En España, por el contrario, solo una fábrica, ubicada en Getafe, cerca de Madrid, se dedica a la producción de los elementos principales del fuselaje. Aquí se realiza el montaje final de los aviones para España, y además se fabrican las alas derechas y ranuras para todas las máquinas.
Esto es sobre el planeador. Pero la producción del caza Eurofighter también incluye motores a reacción de turbina de gas de derivación desarrollados y fabricados conjuntamente. Con este fin, se estableció el consorcio EuroJet Turbo GmbH, con sede en Hallbergmoos, cerca de Múnich, Alemania. Inicialmente, incluía las siguientes empresas de cuatro países socios: Rolls-Royce plc de Derby en el Reino Unido, Motoren- und Turbinen-Union GmbH (MTU) Aero Engines AG de Allah en los suburbios del noroeste de Munich, Fiat Aviazione de Rivalta di Torino (en las afueras de Turín) de Italia y Sener Aeronáutica de España. Esta última empresa está actualmente representada en el consorcio Eurojet por Industria de Turbo Propulsores (ITP), propiedad de Sener. La planta de ITP está ubicada en Zamudio, en el norte de España. A su vez, Fiat Aviazione en Italia se transformó en Avia SpA con las mismas plantas en Rivalta di Torino, 72% propiedad del holding financiero Space2 SpA de Milán, y el 28% restante de Leonardo SpA.
El motor que impulsa el Eurofighter, el EJ200, también es el resultado de un esfuerzo de diseño colaborativo. La distribución de la participación en los costes, trabajos y beneficios de los distintos países es la misma que en el caso del planeador: Alemania y Gran Bretaña 33% cada uno, Italia 21% y España 13%. El EJ200 tiene un ventilador de tres etapas completamente "cerrado", es decir, cada etapa tiene un disco integral con paletas y un compresor de baja presión de cinco etapas en el otro eje, en el que tres etapas tienen forma de "Cierre". Todos los álabes del compresor tienen una estructura monocristalina. Uno de los timones del compresor de alta presión tiene un control de paso para controlar el flujo contra la bomba. Ambos ejes, de baja y alta presión, son accionados por turbinas de una sola etapa. La cámara de combustión anular tiene un sistema de enfriamiento y control de combustión. En la versión actual, el empuje máximo del motor es de 60 kN sin postcombustión y de 90 kN con postcombustión.
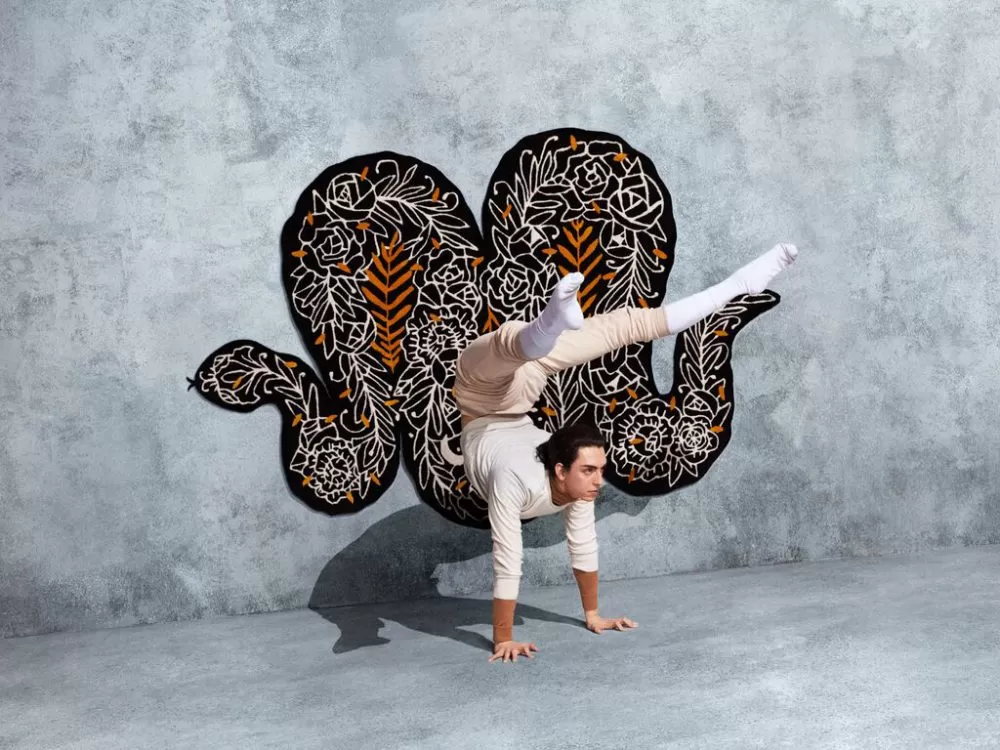