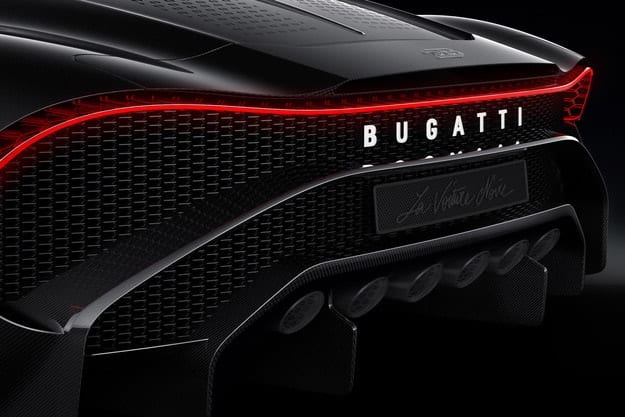
Bugatti: impresión 3D en el corazón de Quirón
El fabricante francés utiliza esta tecnología en 2018 para el modelo Chiron Sport.
Desde 2018, un fabricante de Molsheim ha estado utilizando la tecnología de impresión 3D para fabricar ciertas piezas de hiperesporte Chiron, como las puntas de escape de titanio Pur Sport y Super Sport 300+.
Al igual que Ettore Bugatti, el fundador de la marca tricolor, que regularmente demuestra innovaciones en el diseño de sus modelos (se lo debemos principalmente a llantas de aleación y un eje delantero hueco), los ingenieros responsables del desarrollo de nuevos modelos Bugatti incluyen las últimas innovaciones. en construcción o ingeniería en sus creaciones. La tecnología de impresión 3D, cuyos beneficios ya son bien conocidos, es uno de ellos.
Bugatti utilizó esta tecnología en 2018 en el modelo Chiron Sport, que luego estaba equipado con puntas de escape de Inconel 718, una aleación de níquel-cromo dura y ligera, especialmente resistente al calor (en este caso, el aluminio se funde). Los siguientes modelos de marca (Divo, La Voiture Noire, Centodieci ...) también se beneficiarán de este proceso de fabricación para vender sus tubos de escape.
Estos elementos creados con la impresión 3D tienen varias ventajas. Por un lado, son más resistentes al calor y eliminan la acumulación de calor creada por el motor W8,0 de 16 litros con 1500 hp, y también son más livianos que las boquillas hechas con el método de producción habitual. (El Chiron Sport pesa solo 2,2 kg, por ejemplo 800 g menos que una boquilla normal).
En el caso del nuevo Chiron Pur Sport, Bugatti produce boquillas de escape de titanio con impresión 3D, y el fabricante indica que esta es "la primera pieza metálica visible impresa en 3D con homologación para el tráfico". Esta boquilla, de 22 cm de largo y 48 cm de ancho, pesa solo 1,85 kg (incluida la rejilla y el mantenimiento), que es aproximadamente 1,2 kg menos que el Chiron "estándar".
El sistema especial de impresión láser utilizado para la impresión 3D consiste en uno o más láseres, que a su vez funden capas de polvo de 3 a 4 micras de tamaño. 4200 capas de polvo de metal se apilan una encima de la otra y se fusionan, formando la boquilla de escape Chiron Pur Sport, que resistirá temperaturas superiores a 650 grados Celsius, proporcionando aislamiento térmico de las partes vecinas gracias a una doble pared exterior.
Antes de una inspección exhaustiva e instalación en un vehículo, estos elementos finalmente estarán recubiertos especialmente. Por ejemplo, Chiron Sport está lijado y recubierto con laca negra con pintura cerámica de alta temperatura, mientras que Chiron Pur Sport y Super Sport 300+ están disponibles en titanio cepillado.
Al garantizar la durabilidad, la ligereza y la estética de las piezas, la tecnología de impresión 3D, aún utilizada principalmente en aeronáutica y espacio, parece haber encontrado finalmente su lugar entre los fabricantes de automóviles, incluso los más exigentes.
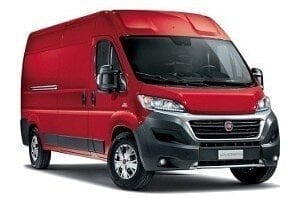
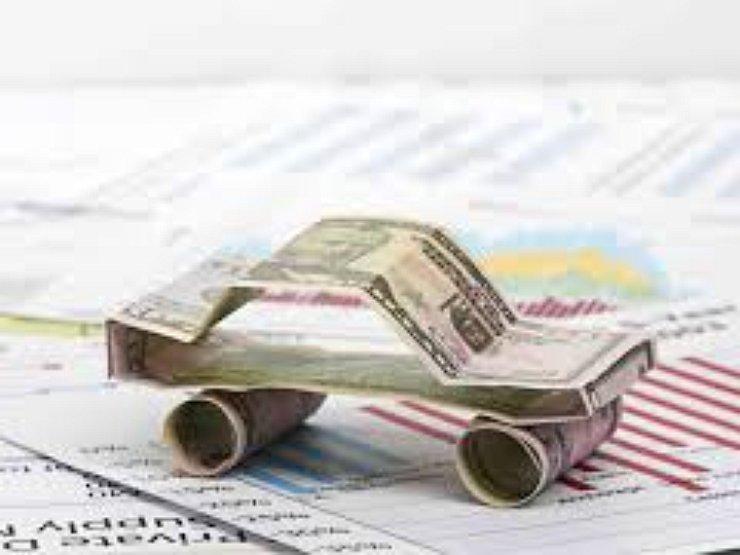