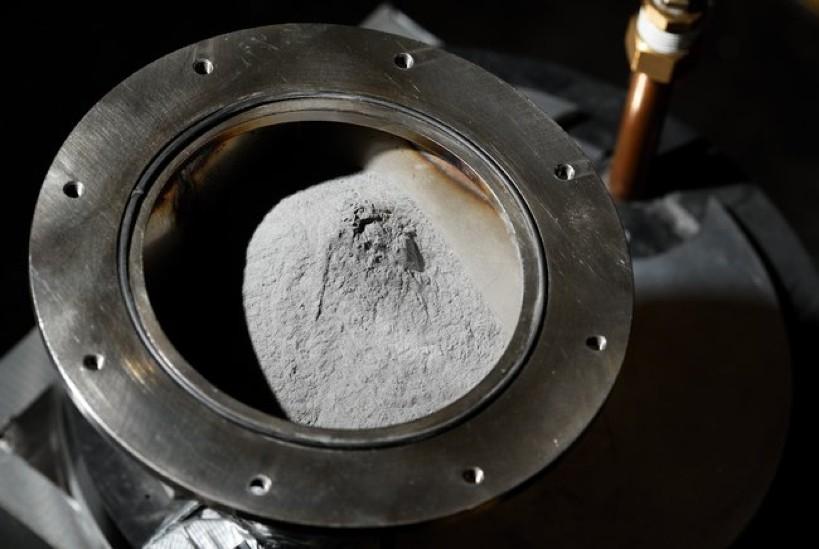
Futuro en polvo
contenido
La empresa sueca VBN Components produce productos de acero utilizando tecnologías aditivas utilizando polvo con aditivos, principalmente herramientas como taladros y fresas. La tecnología de impresión 3D elimina la necesidad de forjar y mecanizar, reduce el consumo de materias primas y ofrece a los usuarios finales una selección más amplia de materiales de alta calidad.
La oferta de componentes VBN incluye, por ejemplo. Vibenita 290que, según la empresa sueca, es el acero más duro del mundo (72 HRC). El proceso de creación de Vibenite 290 consiste en aumentar gradualmente la dureza de los materiales hasta. Una vez que se imprimen las piezas deseadas a partir de esta materia prima, no se requiere más procesamiento que el rectificado o la electroerosión. No requiere corte, fresado o perforación. Así, la empresa crea piezas con dimensiones de hasta 200 x 200 x 380 mm, cuya geometría no se puede producir con otras tecnologías de fabricación.
El acero no siempre es necesario. Un equipo de investigación de HRL Laboratories ha desarrollado una solución de impresión 3D. aleaciones de aluminio con alta resistencia. Se llama método nanofuncional. En pocas palabras, la nueva técnica consiste en aplicar polvos nanofuncionales especiales a una impresora 3D, que luego se "sinterizan" con un láser en capas delgadas, lo que conduce al crecimiento de un objeto tridimensional. Durante la fusión y la solidificación, las estructuras resultantes no se destruyen y conservan toda su fuerza debido a que las nanopartículas actúan como centros de nucleación para la microestructura prevista de la aleación.
Las aleaciones de alta resistencia, como el aluminio, se utilizan ampliamente en la industria pesada, la tecnología de aviación (por ejemplo, fuselaje) y las piezas de automóviles. La nueva tecnología de nanofuncionalización les otorga no solo una alta resistencia, sino también una variedad de formas y tamaños.
Suma en lugar de resta
En los métodos tradicionales de metalurgia, el material de desecho se elimina mediante mecanizado. El proceso aditivo funciona a la inversa: consiste en aplicar y agregar capas sucesivas de una pequeña cantidad de material, creando piezas XNUMXD de casi cualquier forma basadas en un modelo digital.
Aunque esta técnica ya se usa ampliamente tanto para la creación de prototipos como para la fundición de modelos, su uso directo en la producción de bienes o dispositivos destinados al mercado ha sido difícil debido a la baja eficiencia y las propiedades insatisfactorias de los materiales. Sin embargo, esta situación está cambiando poco a poco gracias al trabajo de investigadores en muchos centros alrededor del mundo.
A través de una minuciosa experimentación, se han mejorado las dos tecnologías principales de la impresión XNUMXD: deposición láser de metal (LMD) yo fusión selectiva por láser (ULM). La tecnología láser permite crear con precisión detalles finos y obtener una buena calidad superficial, lo que no es posible con la impresión por haz de electrones (EBM) 50D. En SLM, la punta del rayo láser se dirige sobre el polvo del material, soldándolo localmente según un patrón determinado con una precisión de 250 a 3 micras. A su vez, LMD utiliza un láser para procesar el polvo y crear estructuras XNUMXD autoportantes.
Estos métodos han demostrado ser muy prometedores para la creación de piezas de aeronaves. y, en particular, la aplicación de la deposición de metal por láser amplía las posibilidades de diseño de componentes aeroespaciales. Pueden estar hechos de materiales con estructuras internas complejas y gradientes que no eran posibles en el pasado. Además, ambas tecnologías láser permiten crear productos de geometría compleja y obtener una mayor funcionalidad de los productos a partir de una amplia gama de aleaciones.
El pasado mes de septiembre, Airbus anunció que había equipado su A350 XWB de producción con impresión aditiva. soporte de titanio, fabricado por Arconic. Este no es el final, porque el contrato de Arconic con Airbus prevé la impresión 3D a partir de polvo de titanio y níquel. partes del cuerpo i sistema de propulsión. Sin embargo, cabe señalar que Arconic no utiliza tecnología láser, sino su propia versión mejorada del arco electrónico EBM.
Es probable que uno de los hitos en el desarrollo de tecnologías aditivas en la metalurgia sea el primer prototipo presentado en la sede del grupo holandés Damen Shipyards en el otoño de 2017. hélice de barco aleación de metal que lleva el nombre VAAMpeller. Después de las pruebas apropiadas, la mayoría de las cuales ya se han realizado, el modelo tiene la posibilidad de ser aprobado para su uso a bordo de los barcos.
Dado que el futuro de la tecnología metalúrgica se encuentra en los polvos de acero inoxidable o en los componentes de aleación, vale la pena conocer a los principales actores de este mercado. Según el "Informe del mercado de polvos metálicos de fabricación aditiva" publicado en noviembre de 2017, los fabricantes más importantes de polvos metálicos para impresión 3D son: GKN, Hitachi Chemical, Rio Tinto, ATI Powder Metals, Praxair, Arconic, Sandvik AB, Renishaw, Höganäs AB , Metaldyne Performance Group, BÖHLER Edelstahl, Carpenter Technology Corporation, Aubert & Duval.
Impresión de hélice WAAMpeller
Fase líquida
Las tecnologías de aditivos metálicos más conocidas actualmente se basan en el uso de polvos (así es como se crea la vibenita antes mencionada) "sinterizados" y fusionados con láser a las altas temperaturas requeridas para el material de partida. Sin embargo, están surgiendo nuevos conceptos. Investigadores del Laboratorio de Ingeniería Criobiomédica de la Academia de Ciencias de China en Beijing han desarrollado un método Impresión 3D con "tinta", que consiste en una aleación de metal con un punto de fusión ligeramente superior a la temperatura ambiente. En un estudio publicado en la revista Science China Technological Sciences, los investigadores Liu Jing y Wang Lei demuestran una técnica para la impresión en fase líquida de aleaciones a base de galio, bismuto o indio con la adición de nanopartículas.
En comparación con los métodos tradicionales de creación de prototipos de metal, la impresión 3D en fase líquida tiene varias ventajas importantes. En primer lugar, se puede lograr una tasa relativamente alta de fabricación de estructuras tridimensionales. Además, aquí puede ajustar de manera más flexible la temperatura y el flujo del refrigerante. Además, el metal conductor líquido se puede utilizar en combinación con materiales no metálicos (como los plásticos), lo que aumenta las posibilidades de diseño de componentes complejos.
Los científicos de la American Northwestern University también han desarrollado una nueva técnica de impresión 3D de metal que es más barata y menos compleja de lo que se conocía anteriormente. En lugar de polvo metálico, láseres o haces de electrones, utiliza horno convencional i materia liquida. Además, el método funciona bien para una amplia variedad de metales, aleaciones, compuestos y óxidos. Esto es similar al sello de la boquilla que conocemos con los plásticos. La "tinta" consiste en un polvo de metal disuelto en una sustancia especial con la adición de un elastómero. En el momento de la aplicación se encuentra a temperatura ambiente. Después de eso, la capa de material aplicada desde la boquilla se sinteriza con las capas anteriores a una temperatura elevada creada en el horno. La técnica se describe en la revista especializada Advanced Functional Materials.
Método de impresión de fase de metal líquido chino
En 2016, los investigadores de Harvard introdujeron otro método que puede crear estructuras metálicas en XNUMXD. impreso "en el aire". La Universidad de Harvard ha creado una impresora 3D que, a diferencia de otras, no crea objetos capa por capa, sino que crea estructuras complejas "en el aire", a partir de metal que se congela instantáneamente. El dispositivo, desarrollado en la Escuela de Ingeniería y Ciencias Aplicadas John A. Paulson, imprime objetos utilizando nanopartículas de plata. El láser enfocado calienta el material y lo fusiona, creando varias estructuras como una hélice.
La demanda del mercado de productos de consumo impresos en 3D de alta precisión, como implantes médicos y piezas de motores de aeronaves, está creciendo rápidamente. Y debido a que los datos del producto se pueden compartir con otros, las empresas de todo el mundo, si tienen acceso a polvo metálico y la impresora 3D adecuada, pueden trabajar para reducir los costos de logística e inventario. Como es sabido, las tecnologías descritas facilitan enormemente la fabricación de piezas metálicas de geometría compleja, por delante de las tecnologías de producción tradicionales. Es probable que el desarrollo de aplicaciones especializadas conduzca a precios más bajos y a la apertura al uso de la impresión 3D también en aplicaciones convencionales.
El acero sueco más duro - para impresión 3D:
El acero más duro del mundo - hecho en Uppsala, Suecia
Película de aluminio para impresión:
Avance en metalurgia: impresión 3D de aluminio de alta resistencia

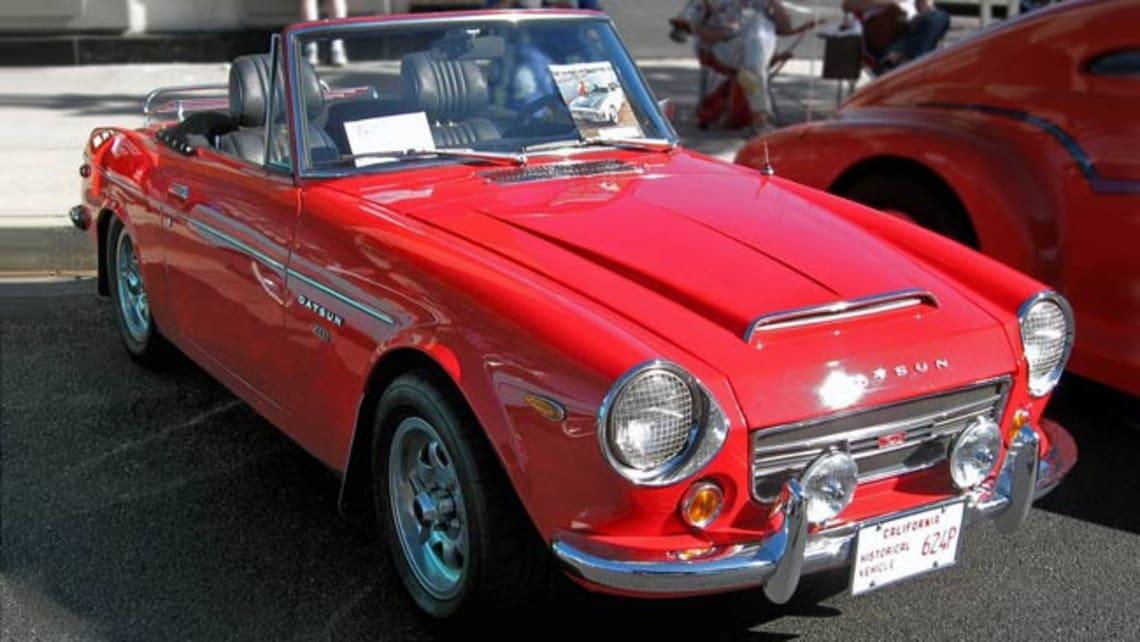
Un comentario
Anónimo
Truco