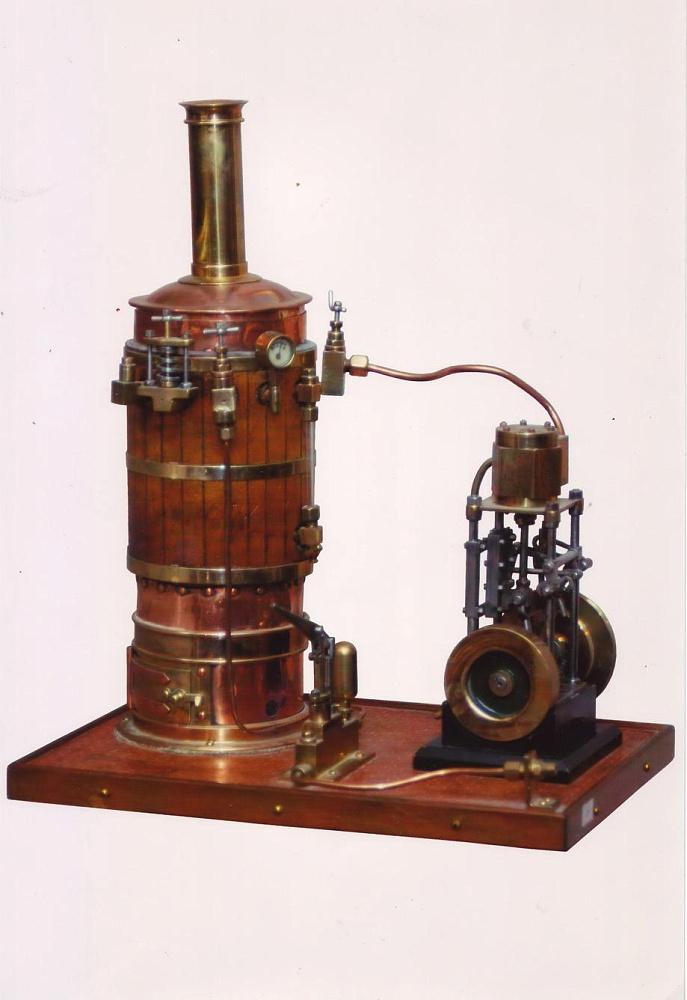
máquina de vapor de madera
Las primeras máquinas de vapor con un cilindro oscilante móvil se crearon en el siglo XIX y se utilizaron para propulsar pequeños barcos de vapor. Sus ventajas incluyen la simplicidad de la construcción. Por supuesto, esas máquinas de vapor no estaban hechas de madera, sino de metal. Tenían pocas piezas, no se estropeaban y eran baratos de fabricar. Se hicieron en versión horizontal o vertical para que no ocuparan mucho espacio en el barco. Estos tipos de máquinas de vapor también se produjeron como miniaturas de trabajo. Eran juguetes politécnicos a vapor.
La sencillez del diseño de la máquina de vapor de cilindro oscilante es su gran ventaja, y podemos sentirnos tentados a hacer un modelo de este tipo con madera. Ciertamente queremos que nuestro modelo funcione y no se quede quieto. Es alcanzable. Eso sí, no lo accionaremos con vapor caliente, sino con aire frío corriente, preferiblemente de un compresor doméstico o, por ejemplo, de un aspirador. La madera es un material interesante y fácil de trabajar, por lo que puedes recrear en ella el mecanismo de una máquina de vapor. Dado que, al construir nuestro modelo, prevemos la parte lateral desmontable del cilindro, gracias a esto podemos ver cómo funciona el pistón y cómo se mueve el cilindro con respecto a los orificios de sincronización. Te sugiero que te pongas a trabajar inmediatamente.
Máquina de operación vapor con un cilindro oscilante. Podemos analizarlos para Foto 1 en una serie de fotografías marcadas de la a a la f.
- El vapor ingresa al cilindro a través de la entrada y empuja el pistón.
- El pistón hace girar el volante a través del vástago del pistón y la manivela de la biela.
- El cilindro cambia de posición, al moverse el pistón, cierra la entrada y abre la salida de vapor.
- El pistón, impulsado por la inercia del volante acelerador, empuja el vapor de escape a través de este orificio y el ciclo comienza de nuevo.
- El cilindro cambia de posición y se abre la entrada.
- El vapor comprimido vuelve a pasar por la entrada y empuja el pistón.
Herramientas: Taladro eléctrico sobre soporte, taladro acoplado a un banco de trabajo, lijadora de banda, amoladora vibratoria, dremel con puntas para madera, sierra de vaivén, englobadora con cola caliente, matriz M3 con portabrocas, taladro de carpintería de 14 milímetros. Usaremos un compresor o una aspiradora para impulsar el modelo.
Materiales: tablero de pino de 100 por 20 milímetros de ancho, rodillo de 14 milímetros de diámetro, tablero de 20 por 20 milímetros, tablero de 30 por 30 milímetros, tablero de 60 por 8 milímetros, madera contrachapada de 10 milímetros de espesor. Grasa de silicona o aceite de máquina, un clavo con un diámetro de 3 milímetros y una longitud de 60 milímetros, un resorte fuerte, una tuerca con una arandela M3. Barniz transparente en aerosol para barnizar madera.
Base de la máquina. Lo haremos a partir de una tabla de 500 por 100 por 20 milímetros. Antes de pintar, es bueno nivelar todas las irregularidades del tablero y los lugares que quedan después de cortar con papel de lija.
Soporte de volante. Lo cortamos de una tabla de pino de 150 por 100 por 20 milímetros. Necesitamos dos elementos idénticos. Después de redondear con una amoladora de banda, lijar 40 a lo largo de los bordes superiores en los arcos y procesar con lija fina en los soportes, taladre orificios con un diámetro de 14 milímetros en los lugares como se muestra en la fig. Foto 2. La altura del carro entre la base y el eje debe ser mayor que el radio del volante.
Llanta de volante. Lo cortaremos de madera contrachapada de 10 milímetros de espesor. La rueda tiene un diámetro de 180 milímetros. Dibuje dos círculos idénticos en la madera contrachapada con un calibrador y córtelos con una sierra de vaivén. En el primer círculo, dibuje un círculo con un diámetro de 130 milímetros coaxialmente y corte su centro. Esta será la llanta del volante, es decir, su llanta. Una corona para aumentar la inercia de una rueca.
Volante. Nuestro volante tiene cinco radios. Se crearán de tal manera que dibujaremos cinco triángulos en la rueda con los bordes redondeados y girados 72 grados con respecto al eje de la rueda. Comencemos dibujando un círculo con un diámetro de 120 milímetros en papel, seguido de agujas de tejer de 15 milímetros de grosor y círculos en las esquinas de los triángulos resultantes. Puedes verlo en Foto 3. i 4., donde se muestra el diseño de la rueda. Ponemos el papel sobre los círculos recortados y marcamos los centros de todos los círculos pequeños con una perforadora. Esto asegurará la precisión de la perforación. Perforamos todas las esquinas de los triángulos con un taladro con un diámetro de 14 milímetros. Dado que un taladro de hoja puede arruinar la madera contrachapada, se recomienda perforar solo la mitad del grosor de la madera contrachapada, luego voltear el material y terminar de taladrar. Una broca plana de este diámetro termina con un diminuto eje que sobresale que nos permitirá ubicar con precisión el centro del orificio perforado en el otro lado de la madera contrachapada. Reflexionando sobre la superioridad de los taladros cilíndricos de carpintero sobre la carpintería plana, cortaremos el resto del material innecesario del volante con una sierra de calar eléctrica para obtener agujas de tricotar efectivas. Dremel compense cualquier imprecisión y redondee los bordes de los radios. Pegue el círculo de la corona con pegamento vicola. Perforamos un agujero de 6 milímetros de diámetro en el centro para poder introducir un tornillo M6 en el centro, obteniendo así un eje de giro aproximado de la rueda. Después de instalar el perno como eje de la rueda en el taladro, procesamos la rueda que gira rápidamente, primero con papel de lija de grano grueso y luego con papel de lija fino. Te aconsejo que cambies el sentido de giro del taladro para que no se afloje el tornillo de la rueda. La rueda debe tener bordes uniformes y girar uniformemente después del procesamiento, sin golpear el costado. Cuando se logra esto, desmontamos el perno temporal y perforamos un agujero para el eje objetivo con un diámetro de 14 milímetros.
Biela. Lo cortaremos de madera contrachapada de 10 milímetros de espesor. Para facilitar el trabajo, sugiero comenzar perforando dos orificios de 14 mm con una separación de 38 mm y luego serrar la forma clásica final, como se muestra en Foto 5.
eje volante. Está hecho de un eje con un diámetro de 14 milímetros y una longitud de 190 milímetros.
Eje del eje. Se corta de un eje con un diámetro de 14 milímetros y una longitud de 80 milímetros.
Cilindro Lo cortaremos de madera contrachapada de 10 milímetros de espesor. Consta de cinco elementos. Dos de ellos miden 140 por 60 milímetros y son las paredes laterales del cilindro. Inferior y superior 140 por 80 milímetros. La parte inferior del cilindro mide 60 por 60 y tiene 15 milímetros de espesor. Estas piezas se muestran en Foto 6. Pegamos la parte inferior y los lados del cilindro con pegamento trenzado. Una de las condiciones para el correcto funcionamiento del modelo es la perpendicularidad del encolado de las paredes y el fondo. Taladre agujeros para los tornillos en la parte superior de la tapa del cilindro. Perforamos agujeros con un taladro de 3 mm para que caigan en el centro del grosor de la pared del cilindro. Taladre un poco la tapa con un taladro de 8 mm para que las cabezas de los tornillos puedan ocultarse.
Pistón Sus dimensiones son de 60 por 60 por 30 milímetros. En el pistón, perforamos un agujero ciego central con un diámetro de 14 milímetros a una profundidad de 20 milímetros. Insertaremos el vástago del pistón en él.
Vástago de émbolo. Está hecho de un eje con un diámetro de 14 milímetros y una longitud de 320 milímetros. El vástago del pistón termina en un lado con un pistón y en el otro lado con un gancho en el eje de la manivela de la biela.
Eje de biela. Lo haremos a partir de una barra de 30 por 30 de sección y 40 milímetros de largo. Perforamos un agujero de 14 mm en el bloque y un segundo agujero ciego perpendicular a él. En este agujero pegaremos el otro extremo libre del vástago. Limpie el interior del orificio pasante y líjelo con una lija fina enrollada en forma de tubo. El eje de la biela girará en el orificio y queremos reducir la fricción en ese punto. Finalmente, el mango se redondea y se acaba con una lima para madera o una lijadora de banda.
Soporte de tiempo. Lo cortaremos de una tabla de pino de 150 por 100 por 20. Después de lijar en el soporte, perfore tres agujeros en los lugares como se muestra en la imagen. El primer orificio con un diámetro de 3 mm para el eje de sincronización. Los otros dos son la entrada y salida de aire del cilindro. El punto de perforación para los tres se muestra en Foto 7. Al cambiar las dimensiones de las piezas de la máquina, los sitios de perforación deben encontrarse empíricamente premontando la máquina y determinando las posiciones superior e inferior del cilindro, es decir, la ubicación del orificio perforado en el cilindro. El lugar donde funcionará la sincronización se lija con una lijadora orbital con papel fino. Debe ser uniforme y muy suave.
Eje de sincronización oscilante. Rematar el extremo de un clavo de 60 mm de largo y redondearlo con una lima o esmeril. Usando un troquel M3, corte su extremo de unos 10 milímetros de largo. Para hacer esto, elija un resorte fuerte, una tuerca M3 y una arandela.
Distribución. Lo haremos a partir de una tira de 140 por 60 por 8 milímetros. Se perforan dos agujeros en esta parte del modelo. El primero tiene 3 milímetros de diámetro. Le clavaremos un clavo, que es el eje de giro del cilindro. Recuerde perforar este agujero de tal manera que la cabeza del clavo quede completamente empotrada en la madera y no sobresalga de su superficie. Este es un momento muy importante en nuestro trabajo, que afecta al correcto funcionamiento del modelo. El segundo orificio de 10 mm de diámetro es la entrada/salida de aire. Dependiendo de la posición del cilindro en relación con los orificios en el soporte de distribución, el aire entrará en el pistón, lo empujará y luego será expulsado por el pistón en la dirección opuesta. Pegue la distribución con el clavo pegado que hace de eje a la superficie del cilindro. El eje no debe tambalearse y debe ser perpendicular a la superficie. Finalmente, taladre un agujero en el cilindro usando la ubicación del agujero en el tablero de tiempo. Todas las irregularidades de la madera, donde estará en contacto con el soporte de distribución, se alisan con una lijadora orbital con lija fina.
Montaje de máquinas. Pegar los soportes del eje del volante a la base, cuidando que queden alineados y paralelos al plano de la base. Antes del montaje completo, pintaremos los elementos y componentes de la máquina con un barniz incoloro. Colocamos la biela en el eje del volante y la pegamos exactamente perpendicular a ella. Inserte el eje de la biela en el segundo orificio. Ambos ejes deben ser paralelos entre sí. Pegue los anillos de refuerzo de madera al volante. En el anillo exterior, inserte un tornillo para madera en el orificio que sujeta el volante al eje del volante. En el otro lado de la base, pegue el soporte del cilindro. Lubrique todas las piezas de madera que se moverán y estarán en contacto entre sí con grasa de silicona o aceite para máquinas. La silicona debe pulirse ligeramente para minimizar la fricción. De ello dependerá el correcto funcionamiento de la máquina. El cilindro está montado en el carro de modo que su eje sobresalga más allá de la sincronización. Puedes verlo en Foto 8. Coloque el resorte en el clavo que sobresale del soporte, luego la arandela y asegúrelo todo con una tuerca. El cilindro, presionado por un resorte, debe moverse ligeramente sobre su eje. Colocamos el pistón en su lugar en el cilindro y colocamos el extremo del vástago del pistón en el eje de la biela. Colocamos la tapa del cilindro y la sujetamos con tornillos para madera. Lubrique todas las partes cooperantes del mecanismo, especialmente el cilindro y el pistón, con aceite para máquinas. No nos arrepintamos de la grasa. La rueda movida a mano debe girar sin resistencia perceptible y la biela debe transferir el movimiento al pistón y al cilindro. Foto 9. Inserte el extremo de la manguera del compresor en la entrada y enciéndalo. Gire la rueda y el aire comprimido moverá el pistón y el volante comenzará a girar. El punto crítico de nuestro modelo es el contacto entre el plato de distribución y su estator. A menos que la mayor parte del aire escape de esta manera, un automóvil diseñado correctamente debería moverse con facilidad, brindando mucha diversión a los entusiastas del bricolaje. La causa del mal funcionamiento puede ser un resorte demasiado débil. Después de un tiempo, el aceite empapa la madera y la fricción se vuelve demasiado. También explica por qué la gente no construía máquinas de vapor con madera. Sin embargo, el motor de madera es muy eficiente, y el conocimiento de cómo funciona el cilindro oscilante en un motor de vapor tan simple permanece durante mucho tiempo.
máquina de vapor de madera
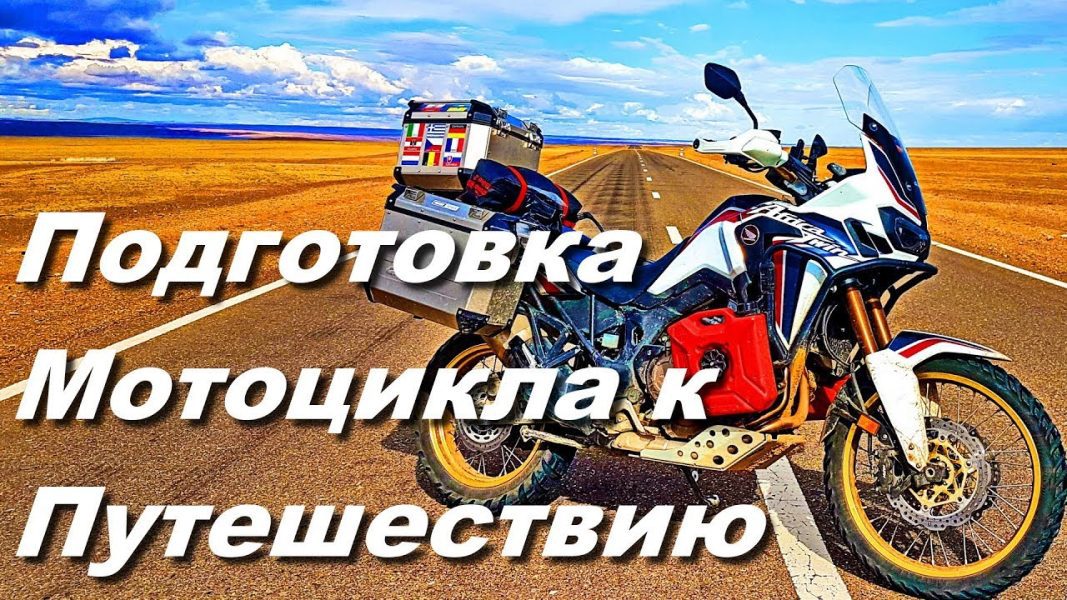
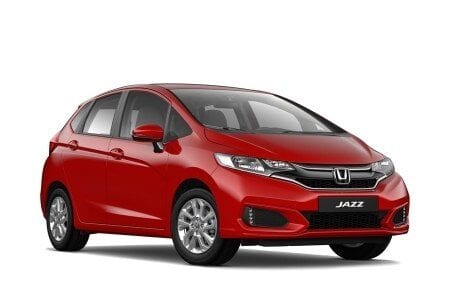